
An extreme failure of this test from a member company’s cable order is shown in Figure 1. Furthermore, one of those specimens must be harvested from insulation adjacent to the conductor shield, where adequate curing is often harder to achieve, yet this is the area that experiences the highest operating temperatures. In addition, three specimens from the inner 25% of the cable insulation must now be tested rather than just one. A statistical review of CTR data, as described earlier, revealed that 120% was a more appropriate, yet still conservative, value. The elongation requirement shown in ANSI/ICEA standards defining adequate curing of some cross-linked polyethylene (XLPE)-based insulation was changed from 175% to 120%. A few of the significant changes to this revision are described briefly in the following paragraphs. Many of the revisions in the 2020 version of CS8 have been added based on the CEC’s findings during the aforementioned review process. These properties are determined via a review of production certified test reports (CTRs) and, for many members, by physical inspection and measurement of completed cable samples prior to cable acceptance. The CEC defines the present level of performance in terms of the physical and electrical properties of the cable that member companies receive from their cable manufacturers. One of the CEC’s recently published specifications is the fifth edition of CS8 “Specification for Extruded Dielectric, Shielded Power Cables Rated 5 Through 46 kV.” This specification is voluntary and is written as a supplement to the American National Standards Institute (ANSI) and Insulated Cable Engineers Association (ICEA) industry standards.Ī key CEC goal is to ensure that the level of cable performance utilities have come to expect over many years of positive field experience is at least maintained or preferably improved at a reasonable cost. utility representatives with more 100 years of extensive field construction and maintenance experience worked on the following publications. Through collaboration, this committee has been able to create specifications that drive manufacturers to build more reliable products and our specifications have been referenced in purchasing specifications all across the world,” said Najwa Abouhassan, manager of Distribution Standards at ComEd and chair of AEIC-CEC. “Each member brings unique experiences that have made our specifications and guides essential to utility engineers. Its affiliations with other electrical engineering organizations and testing facilities allow it to gather information about cable systems’ operation and reliability, and apply best practices across the electric utility industry. The CEC also monitors the production of cable manufacturers and acts as an advocate for electric utilities. The AEIC’s cable specifications and guides give vital information for manufacturers of electrical cables, while providing the electric industry and other electrical system users with clear and concise data to specify underground cables, connectors, and whole underground systems, as well as guiding the proper installation, maintenance, and operation of these systems. Today, AEIC’s Cable Engineering Committee (CEC) continues to develop and improve underground electrical systems by publishing detailed cable specifications and guides that are followed by utilities, architects, engineers, and developers worldwide. Some of the earliest urban applications of the Edison system were the installation of underground electrical cable systems. The group, which is one of the oldest organizations in the electric energy industry, encourages research, and the exchange of technical information and best practices, through a committee structure staffed with experts and volunteer engineers from AEIC member companies.

The Association of Edison Illuminating Companies (AEIC) was founded in 1885 by Thomas Edison and his associates.

Two recently updated specifications and guides provide system designers and engineers with important information to ensure a lifetime of satisfactory performance for these systems.
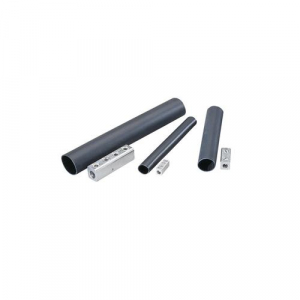
Underground electrical cable systems are used by power companies around the world.
